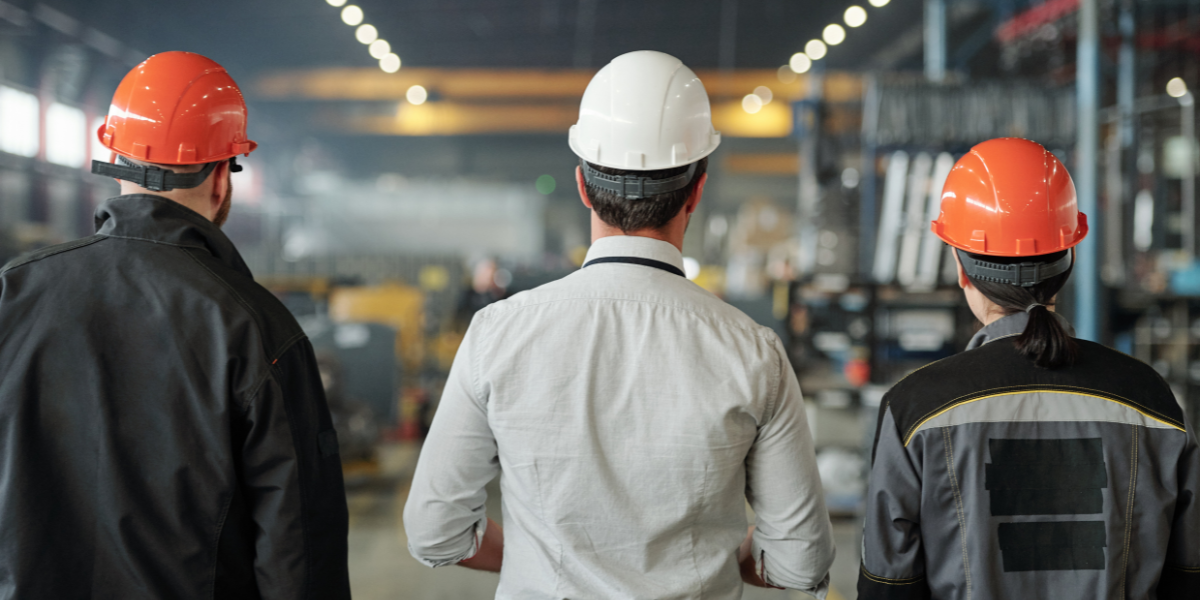
Why We Need to Rethink Manufacturing Plant Culture
The manufacturing environment involves two critical cultures of the workforce. One group spends their time in the plant managing the floor operations, and the other in the office managing accounting, sales, marketing, etc. However, they represent the overall company culture — disjointed or united.
Manufacturing Plant Culture vs. Office Culture
Often the plant workforce is labeled as manual unskilled laborers that require constant supervision to “stay busy.” But today, the manual workforce has been replaced in all areas possible to reduce labor costs, improve efficiency, and increase outputs. Complex control systems, lean manufacturing, and six sigma are prominent on the plant floors. Digital and robotic factories can be found across the country. These advancements demand that managers and supervisors be much more than overseers or babysitters.
Progressive and constant training and hiring of experienced and educated members are necessary for modern manufacturing operations. Are the smartest guys in the room only sitting in the front office? Not in today’s manufacturing culture. There should be a balance of education and application in both areas.
So will hiring the most educated workforce solve all the culture clashes? Ken Iverson is known as a business maverick with an astonishing track record of success, including building Nucor from ground zero to an empire.In the epilogue of Mr. Iverson’s book “Plain Talk,” he discusses the possible cure for the common MBA. He points out his learning curve of forming teams of MBAs hired from top business schools.
“They’ve come to us, a degree in hand, and ready to conquer the world. We soon found out they couldn’t conquer the basics of managing a department.”
Leadership will always remain the most critical educator for the operation. Some will be found in the office, and some on the plant floor.
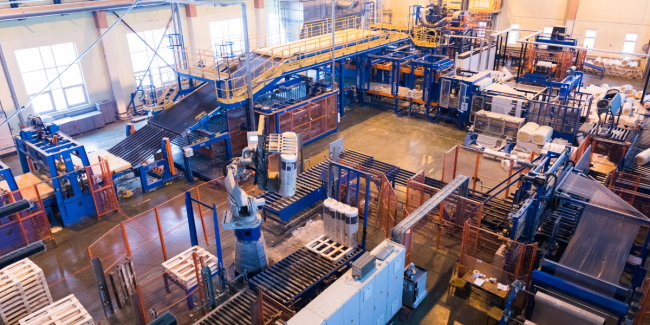
IntoCeramics specializes in manufacturing consulting — contact us today to get started.
The Key to Optimizing Plant Efficiency Is Building a Strong Culture
Manufacturing plant culture is fueled by productivity. Time is money. How many pieces per hour did we run, how much downtime was involved, how much overtime was required, and so on. The overall efficiency on the plant floor is a key metric to the unit cost. Manufacturing leadership must have an engaged sense of urgency to meet production demands and order requirements. Quick decisions are required that impact quality, safety, and output. It requires years of experience for most of these quick decisions to yield positive results.
Does office culture not require the same sense of urgency? Sure, it does. The manufacturing team often struggles with this, as it seems when they go to the front office, people are talking, laughing, in meetings, and so on, and little is getting done. The office group is under constant deadlines to deliver cost data, budget reports, sale figures, forecasts, dealing with complaints, and ultimately forming the strategy for several paths forward. Again, quick decisions are required that impact the organization’s overall wellness. And yet again — same as the plant team — this requires years of experience to make the majority of these decisions benefit the company.
Creating Unity Between the Plant and Office
Bridging the gap between the two cultures in the manufacturing plant is necessary so that all are pulling the rope in the same direction. Here are some tips from over 20 years of working in both environments.
- Merge: Constantly create teams that intertwine the two cultures by having members from both groups. This can be painful sometimes, but stick to your guns so that all involved understand their roles. You will find most have the same objective of improving the company’s performance while improving their status in the workplace.
- Engage: Allow your office team to get out on the plant floor to meet, greet, and develop a good understanding of the overall process flow. The same is needed for the plant team to understand what is required from the office group. Walk crews through the office, explaining the different groups and their functions.
- Respect: At times, the operator cleaning the pits out has just as vital a role as the company president. If this operator does not complete the task at hand promptly, accurately, and safely, the plant will suffer. Show respect to all on your team. Teach your entire team that respect is the cornerstone of your business.
Creating unity between the plant and the office will speak volumes about the organization’s overall culture.
Learn More from The Manufacturing Industry Experts at IntoCeramics
Transforming a company’s culture requires ongoing effort, especially among its manufacturing leaders, and it cannot simply be delegated. By prioritizing safety, efficiency, teamwork, and quality, manufacturing plant culture can help to optimize plant efficiency and drive long-term success.
With their expertise and experience, the manufacturing consultants at IntoCeramics can provide valuable insights into how to best utilize the latest technology and processes for your business. They also offer educational resources and tools to help you make informed decisions about your operations. From product design to production, our manufacturing consulting company has the knowledge and resources to help you succeed.