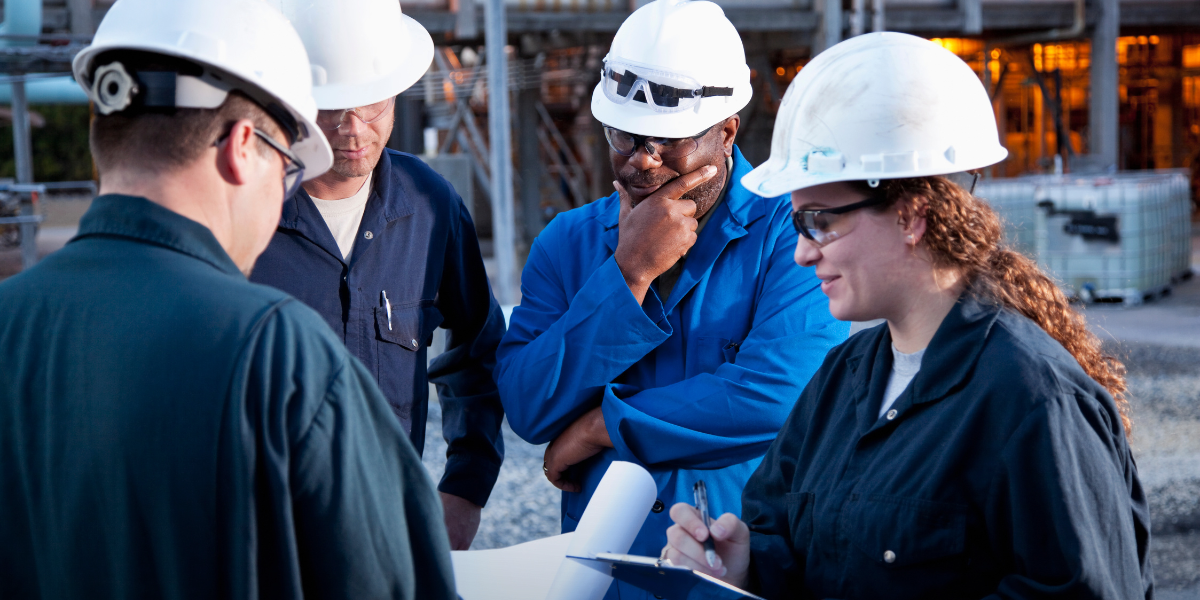
Developing an Atmosphere of Trust & Integrity
Trust and integrity might sound like abstract ideals, but they’re the backbone of any well-run plant. Without them, problems get hidden, communication breaks down, and progress stalls. With them, real improvement becomes possible.
Why Trust and Integrity Matter in Manufacturing
Creating a culture of trust and integrity on the plant floor isn’t a soft skill; it’s a strategic advantage. How we respond to problems, how freely people share information, and how leadership sets the tone can make or break day-to-day operations.
One way to think about this is through the lens of “full disclosure.”
Full disclosure as defined in computer security means to disclose all the details of a security problem that are known. It is a philosophy of management completely opposed to the idea of security through obscurity.
The theory behind this example involves exposing vulnerabilities openly so that quicker fixes are found and better security prevails.
In real estate terms, full disclosure is the act of providing all material information about an article or property intended or proposed to be transferred, which may influence the decision of the buyer or proposed buyer.
In accounting principles, full disclosure states that you should include in an entity’s financial statements all information that would affect a reader’s understanding of those statements.
Consider these definitions and their relevance to manufacturing now.
Is Full Disclosure at Work, or is it Being Avoided?
Do we recognize that problems are more evident when the plant culture endorses full disclosure compared to sweeping everything under the rug?
Do we encourage our team to openly provide all the information needed about a concern or problem instead of just handling it? Is the environment such that critical information impacting the plant’s ability to excel is withheld?
Do lab test results show enough repeatability to enter the manufacturing arena?
Leading by Example Builds the Foundation
A culture of trust and integrity doesn’t develop overnight, but it starts with leadership modeling the behavior they want to see. When leaders are honest about shortcomings or project risks, they give permission for their team to do the same. Over time, this becomes embedded in how problems are addressed and improvements are implemented.
Trust isn’t just about being honest when it’s easy. It’s about sharing difficult truths when doing so might delay a deadline, challenge a decision, or highlight an oversight. It’s about prioritizing the long-term health of the plant over short-term appearances.
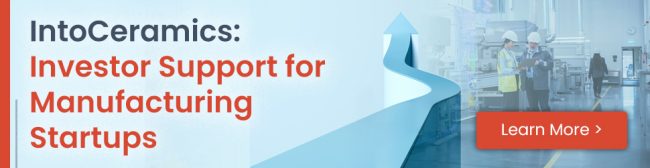
When Truth is Avoided, Trouble Grows
We’ve all seen what happens when problems are hidden until it’s too late. Equipment failures that could have been minor become major shutdowns. Customer complaints pile up because quality issues were never raised. Teams burn out because no one wants to admit the schedule isn’t realistic.
Honest communication backed by leadership support is the best preventative maintenance a plant can have. So ask yourself: what behaviors are you rewarding? What gets overlooked? And where can you create space for your team to speak up without fear?
Ready to Build a More Transparent Plant Culture?
IntoCeramics has decades of experience helping manufacturing teams navigate plant culture challenges that impact real-world performance. We offer support in toll manufacturing, ceramic consulting, analytic testing, and coaching plant leadership teams. Let’s talk about how to make your plant a place where honesty isn’t punished and information flows freely.
Contact us today to learn more about our approach to practical, people-focused manufacturing consulting.