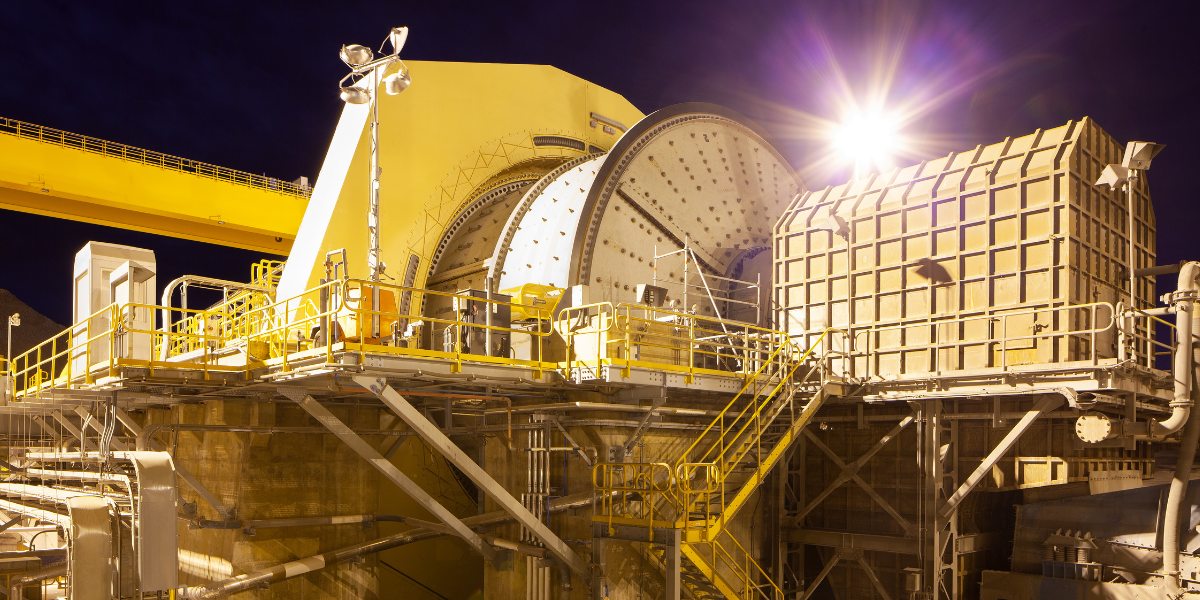
Ball vs. Jet Milling: Dry Techniques Explained
In ceramics manufacturing and other industrial processes, achieving the right particle size is essential for creating high-quality products. Two common dry milling techniques used to achieve this are ball milling and jet milling. While both methods can reduce particle size, each has unique advantages and limitations that make them suitable for different applications. Keep reading to learn more from the experts at IntoCeramics.
What is Ball Milling?Ball milling is a traditional and widely used method for grinding materials into fine powders. It involves using a rotating cylindrical drum filled with grinding media, such as ceramic or steel balls, which crush the material as the drum rotates. The ball mills can be lined in various construction of materials from ceramic to rubber to polyurethane.
One of the key benefits of ball milling is its ability to handle a variety of materials, including ceramics, minerals, and metals. It’s particularly effective for larger, harder particles. Typically, dry ball milling can achieve 100% -44μm and around a d50 of 5 μm at best, making it ideal for medium to coarse particle sizes. Ball mills have been around for material years as a fundamental method of grinding minerals. Many studies and years of testing help determine the size media to material ratio, media type, media loading, media shape, etc.
However, ball milling has limitations when it comes to achieving ultra-fine particles. While it can provide a uniform grind, it may not reach the finer particle sizes required for some applications without prolonged milling times.
What is Jet Milling?
Jet milling, on the other hand, uses high-velocity air or steam to create fine powders. Instead of grinding with media, the material is pulverized by particle collisions inside a chamber where high-pressure jets are introduced. This method is particularly well-suited for achieving finer particle sizes than ball milling services can offer.
In terms of performance, jet milling can typically reach a d50 of 2.5μm when milling in air and less than 1μm when using steam jet milling. This makes it the preferred choice for ultra-fine powders and applications requiring a precise, controlled particle size distribution.
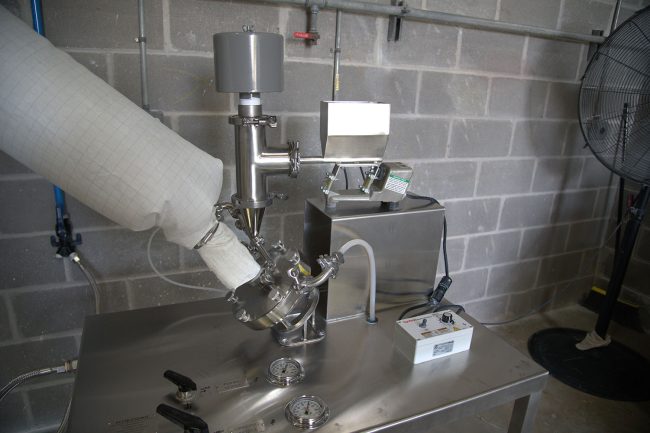
Ball Milling vs. Jet Milling: Key Differences
When it comes to ball milling and jet milling, knowing which one to use can make all the difference for your project. Let’s compare the two:
- Particle Size – While ball milling is effective for producing medium-coarse powders, jet milling excels at achieving much finer particle sizes.
- Material Hardness – Ball milling can handle harder materials more efficiently, while jet milling is more suitable for softer or more brittle substances.
- Energy Consumption – Jet milling tends to consume more energy than ball milling, especially when using steam, but it compensates with its ability to reach ultra-fine particles in a shorter time frame.
- Cost – Ball milling is generally more cost-effective for medium-coarse milling, while jet milling, though more expensive, delivers precision for ultra-fine particle requirements.
Choosing the Right Technique
Choosing between ball milling and jet milling depends largely on the specific particle size and material properties you need to achieve.
For applications where a d50 of 5um is acceptable, ball milling offers a reliable and cost-effective solution. However, if your application demands finer particles, particularly in the sub-micron range, jet milling provides the precision you need.
Tackle Your Dry Milling Needs with IntoCeramics
At IntoCeramics, we’ve got you covered with the right toll manufacturing equipment for both ball milling and jet milling. From coarse powders to ultra-fine particles, our team of experts knows how to optimize the process for your specific material. With our advanced line of machinery and years of experience, we can help you achieve the perfect particle size for your project.
Reach out to us today to see how we can put our dry milling capabilities to work for you.