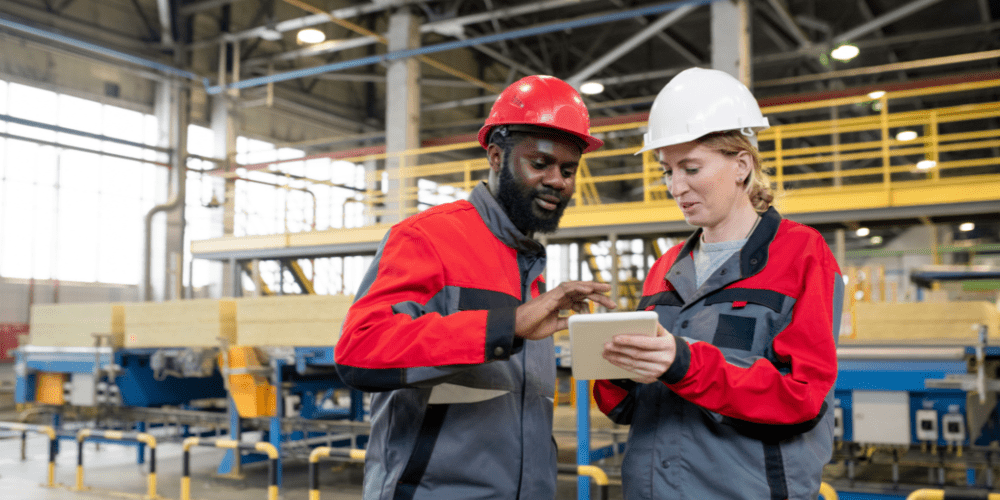
The Plant Manager’s Survival Guide for Rookies and Veterans
Plant managers have complex and demanding jobs. They must manage production, optimize processes, and ensure safety regulations are followed. This guide provides invaluable advice and strategies for navigating this challenging role successfully. It is a comprehensive resource that addresses the key aspects of plant management from start to finish, helping managers save time and energy while achieving maximum efficiency in their work.
This blog is written for two core groups: the first-time plant manager of any operation and the experienced plant manager in a new operation.
The First-Time Plant Manager – Stick to The Fundamentals
Whether you are promoted from within or hired from the outside, this is your first time as a plant manager of an operation. What have you always wanted to be? Maybe — or perhaps you are testing the waters because the title and pay sound great. Either way, you should stick to the fundamentals of your role, or failure is an option.
1) Practice Humble Leadership
Do not assume you are the smartest person in the room. Undoubtedly you are surrounded by experienced supervisors and operators that know much more about the process and product than you do at this point. Do not underestimate their ability to make or break you in the first year.
Figure you have a grace period of about six months to learn the ropes and earn respect — or not. After six months, you are either headed forward or possibly outward. Listen to those that know and be a student of the process and the product. Study on and off the field, take notes, and ask many questions.
2) Be Available and Be Visible
Do not get wrapped up in corporate meetings, conference calls, and endless emails that keep you from being on the plant floor. Your management and operations teams need to see you engaged with the process. They spend most of their day in the operation, and here lies the heartbeat of the plant. Advise those upstream that you are learning the people and the process first in your new role.
3. Commit to Your Employees
Respect all and learn names. The person cleaning the floors has a role just as you do, or the plant suffers. Speak to your group daily and learn their names. Talk about life in and outside the plant and be genuine. Do not just go through the motions with easy distractions. Be real, and it will show; be fake, and it will show more.

The Experienced Plant Manager – You Still Need Help
Most of the time, the last plant manager got fed up quickly or got canned. So you are the next leader brought in to make sense of the chaos.
1. Adopt a Growth Mindset
Regardless of the history given to you by corporate, you must be strong enough to evaluate the people and process and make your own decisions. Threats and replacing staff members right off the bat assumes you have all the answers. Are you prepared to run the plant on your own? Granted, after a few months, more than likely, you will need to make some changes as the last plant manager did not fail alone. However, give all the benefit of the doubt and go in with no preconceived notions.
2. Spot Your Go-To Members Quick
The best plant manager for your job may already be in the plant and was either overlooked or does not want full responsibility for the plant. This person and other key manufacturing leaders are easy to spot. They are the “problem solvers.” Equipment issues, personnel problems, and quality concerns engage them daily for resolutions. No matter your education or years of experience, these are your critical allies to fight the battle day in and day out.
3. Listen and Lead
Pay attention and listen to the culture of the plant and the people. The culture may need a remodel or total rebuild, and that’s your core function. Build the manufacturing plant culture needed, and great things will happen quickly. Promote engagement, respect, full disclosure, and loyalty, and the culture will have a great foundation.
“Followers who tell the truth and leaders who listen to it are an unbeatable combination.” – Warren Bennis
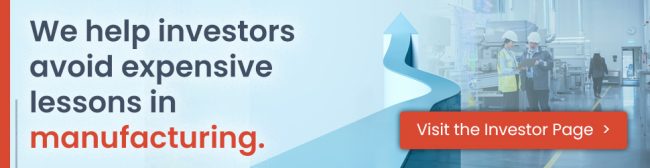
Optimize Your Plant Performance with IntoCeramics
IntoCeramics provides comprehensive solutions to optimize your plant performance. Our experienced team of manufacturing consulting experts can help you identify and solve operational issues, reduce costs, increase efficiency, and improve the overall quality of your products. We can provide customized strategies to meet your specific needs, as well as offer insights into the latest technologies and best practices in the industry. With our tailored approach and expertise, we can help you achieve higher productivity while reducing waste and energy consumption.
On the Plant Floor is a manufacturing guide for both the new, inexperienced leader and the seasoned plant manager. Click the link below to read now!
Contact IntoCeramics today to learn more about plant management.