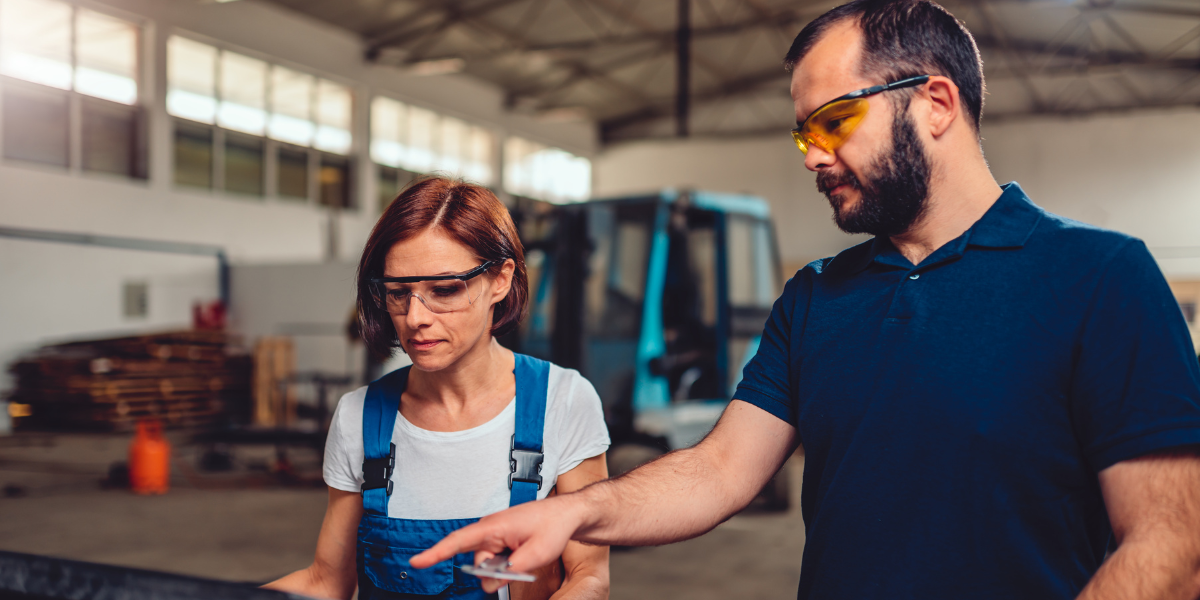
Manufacturing Plant Management Tips from the Front Lines
When you walk into a manufacturing plant for the first time, what do you look for to determine if the plant is managed well and has effective leadership? First impressions and lasting judgments say much about your engagement and pride in the facility and the culture you have built.
How To Keep Your Manufacturing Plant Running Smoothly
A well-led plant is a quiet place, with no extra noise over and above process equipment. Even those who enter your facility and do not have any knowledge of the production process or manufacturing experience will take notice.
We know too well the chaos that can be involved on the plant floor. Equipment is down, personnel are scrambling, and there appears to be no sense to the madness. A factory that is full of drama and allows chaos to unfold before a visitor’s eye indicates a poorly managed plant.
A well-run plant may seem dull as everything flows like a fine-tuned engine. The drama has been replaced by developing a culture that anticipates crises and converts them into a routine. We have often said to ourselves that we wish nothing more than to be bored on the plant floor… we’ll get our excitement elsewhere.
Best Practices for Successful Manufacturing Plant Management
Here are some points to ensure you and your team make good first impressions and foster lasting judgments about your plant.
Keeping Housekeeping a Routine
This is critical to enforce into the culture as routine. A clean plant sends a powerful message about standards and expectations. When housekeeping is second nature, it reinforces pride and discipline in every task.
Maintaining a Culture of Organization
Ensure everything has a place, stacked straight, leveled, and squared. Visual order eliminates waste and hesitation, setting the tone for how people treat materials, tools, and shared spaces.
Keeping Equipment in “Looks New” Condition
Wipe down, paint, and do not permit the cabinets or panels to be cluttered with items that do not belong there. Your operator or other staff may be unable to learn all the intrinsic details to maximize the equipment’s performance, but they can keep it clean and organized.
Setting the Standard in Management Offices
If desks are covered, the floors are a mess, and the place is a wreck, it is a flawed culture. Offices should reflect the same level of care and order you expect from the shop floor. They are part of the plant, not an exception to its values.
Making Plant Restrooms a Point of Pride
The condition of your plant’s bathrooms is an area that you should be proud of and not ashamed for visitors to utilize. (People notice this area as much as any.)
Dressing the Part on the Plant Floor
Being on the plant floor is a dirty job in most operations. However, requiring your management team to look professional is a must. Anyone should be able to spot a manager on the plant floor and distinguish them from the rest of the workers. A shirt with a collar and Docker-style pants will suffice. Anything beyond this, and you might be afraid to get down and get dirty.
Beyond the obvious ease of dressing yourself, how do you achieve these conditions? You won’t do it by fiat-you can’t speak these things into existence. You have to build and be a part of a culture that makes these conditions expected and normal.
Building a Culture Where Good Practices Stick
One of the ways to do that is to spread the pain. “Spreading the pain” is another way of saying that all should shoulder the burden jointly so that all may share in the rewards of success. Now that is an easy concept to understand, but your ability to pull it off successfully is somewhat harder. Is your organizational culture up to it?
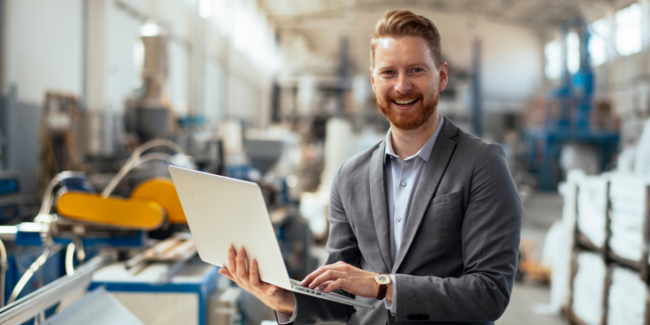
Contact IntoCeramics today to learn more about plant management and ceramic consulting!
Replacing Silos with Sequences
We grew to remove the term “departments” and replace it with “sequences.” Departments can signal a division of groups that builds walls and does not interact with other areas as needed. While one “department” may be performing magnificently, the department before them or after them is struggling.
In unison with the manufacturing plant culture, here again, the whole will be greater than the sum of its parts. The flow in the plant is hindered when certain areas are building empires and others are falling.
Department vs. Sequence
“Department” can create independence rather than unity. Using the term “sequence” makes a known belief that each area is only a part of the whole.
Think of sequence as a chain on a motor. If one link in the chain breaks, the motor stops, as well as production. Sequence A provides a service to sequence B and sequence B to sequence C, and so on. If any sequence breaks down or has quality defects, it directly impacts the other sequences — and the process as a whole.
“Spreading the pain” or making all responsible for the ultimate results will encourage sequences to share information and process improvement techniques throughout the plant. The supervisor of sequence B, who has great individual results, soon becomes involved with other sequences to champion their efforts.
Positive Pressure and Clear Questions
Do not underestimate the power of persistence and positive competition in the plant. It encourages others to excel by empowering and holding them accountable for all areas of their sequence. At the plant manager level, ask some basic questions repeatedly and follow these guidelines to be most effective:
- What needs to be done?
- What is right for the plant? Focus on what is right instead of who is right.
- Help develop the action plans.
- Take responsibility for decisions.
- Take responsibility for communicating.
- Focus on the opportunities more than the problems.
- Run productive meetings; keep them concise and infrequent.
- Focus on strengths more than weaknesses. Ask “what can a man do” instead of listing everything “he cannot do.”
- Say “we” much more than “I.”
“Spreading the pain” to maximize results and build the culture may not be the most popular avenue to take, and good-performing supervisors might bristle. However, having certain groups that excel while others fail is not spreading the talent and knowledge needed for a great culture and a great plant.
Learn more in our Plant Manager’s Survival Guide!
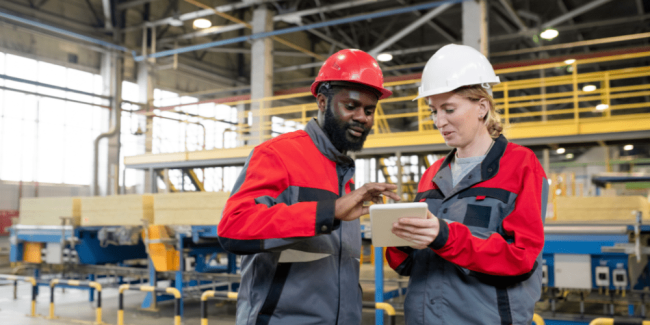
Planning for New Manufacturing Sites and Facilities
Launching a new manufacturing plant or expanding into additional manufacturing facilities calls for more than floor space and equipment. It takes careful attention to supply chains, workforce structure, and plant management methods that apply from day one. IntoCeramics works with plant managers to guide these setups with practical strategies…especially when introducing new technologies or aligning asset management practices across teams.
From selecting layout options to deciding how different departments interact, early decisions shape long-term outcomes. Our manufacturing consultants support teams standing up new facilities with the same attention to detail we bring to established operations.
How IntoCeramics Helps Manufacturing Plant Managers Strengthen Operations
Leadership in manufacturing facilities shapes how teams collaborate, how assets are used, and how raw materials move through production. IntoCeramics’ manufacturing consulting supports plant managers working to improve coordination, raise accountability, and bring consistency across different departments.
Assembly plants often face pressure to balance quality control, asset management, and daily decision making. The pace of operations makes it easy to lose focus. The manufacturing leaders at IntoCeramics helps managers apply clear practices that support operational efficiency and minimize disruption. Our work focuses on practical improvements. That includes setting expectations on the floor, building communication between sequences, and reinforcing habits that reduce variability across shifts.
Contact our team or visit our blog for more insights.
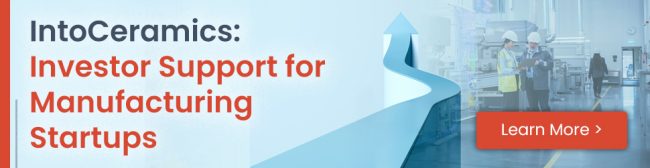